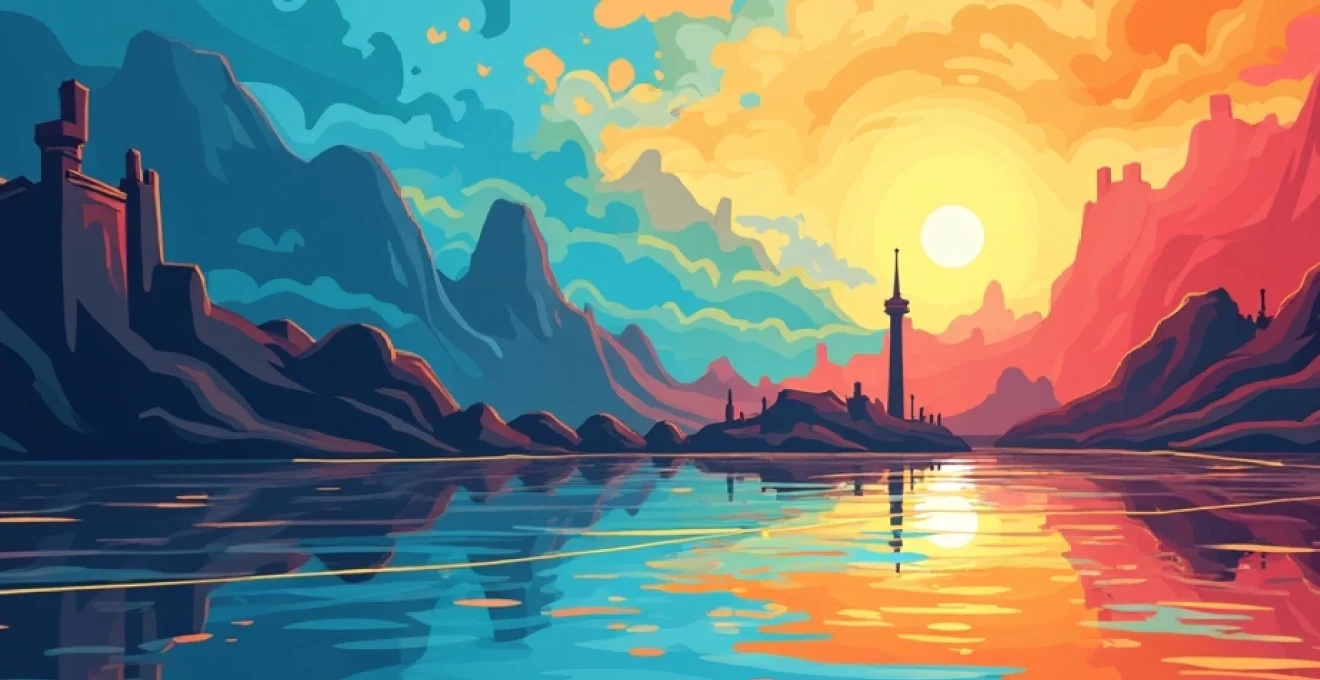
The printing industry is undergoing a significant transformation, driven by technological advancements and changing market demands. At the forefront of this evolution is hybrid printing equipment, which combines the best features of digital and conventional printing methods. This innovative approach is reshaping the landscape of print production, offering unprecedented versatility, efficiency, and quality. As businesses strive to meet diverse customer needs while maintaining competitive edges, hybrid printing systems are emerging as a game-changing solution.
Hybrid printing offers versatility across print jobs
One of the most compelling advantages of hybrid printing equipment is its remarkable versatility. These systems are designed to handle a wide range of print jobs, from short runs to high-volume production, with equal proficiency. This flexibility allows print service providers to adapt quickly to changing customer requirements without the need for multiple specialized machines.
Hybrid presses combine the strengths of digital printing, such as variable data capabilities and quick turnaround times, with the high-quality output and cost-effectiveness of conventional printing methods for longer runs. This convergence of technologies enables printers to offer a broader spectrum of services to their clients, effectively expanding their market reach and potential revenue streams.
Moreover, the ability to switch seamlessly between digital and conventional printing modes on a single machine means that print shops can optimize their workflow for each job. This adaptability is particularly valuable in today's fast-paced market, where customization and personalization are increasingly in demand.
Combining digital offset technologies boosts productivity
The integration of digital and offset technologies in hybrid printing systems has led to significant productivity gains across the industry. By leveraging the strengths of both methods, printers can achieve higher output rates while maintaining exceptional quality standards.
Faster turnaround times on short runs
Digital components of hybrid presses excel at handling short print runs with rapid turnaround times. This capability is crucial in meeting the growing demand for just-in-time production and personalized print materials. With hybrid equipment, printers can quickly set up and execute small jobs without the lengthy makeready processes associated with traditional offset printing.
Maintain high quality on longer runs
For longer print runs, the offset components of hybrid systems come into play, delivering the high-quality, consistent results that offset printing is known for. This dual-capability ensures that print shops can maintain the quality standards expected by their clients, regardless of the job size or complexity.
Seamless switching between print methods
Perhaps the most innovative aspect of hybrid printing equipment is the ability to switch between digital and offset printing methods on the fly. This seamless transition allows for optimal resource utilization and enables printers to combine the benefits of both technologies within a single print job. For instance, a long run of static content
can be printed using offset, while variable data elements are added digitally in the same pass.
Hybrid printing systems represent a paradigm shift in production efficiency, allowing printers to adapt their processes in real-time to meet diverse client needs.
Hybrid presses provide cost efficiency gains
The economic benefits of hybrid printing equipment are substantial and multifaceted. By consolidating multiple printing capabilities into a single system, print service providers can realize significant cost savings across various aspects of their operations.
Reduced makeready waste lowers expenses
One of the most immediate cost benefits of hybrid presses is the reduction in makeready waste. Traditional offset printing often requires a considerable amount of paper and ink to be used during setup, resulting in waste that eats into profit margins. Hybrid systems minimize this waste by leveraging digital printing for short runs and setup processes, significantly reducing material costs.
Inline finishing options cut postpress costs
Many hybrid printing systems come equipped with inline finishing options, such as cutting, folding, and binding. This integration of postpress processes into the printing line eliminates the need for separate finishing equipment and reduces labor costs associated with handling printed materials between processes. The result is a more streamlined production flow and lower overall production costs.
Decreased labor requirements improve margins
Hybrid presses are designed with automation in mind, reducing the need for manual intervention throughout the printing process. This automation translates to lower labor costs and improved operational efficiency. Print shops can reallocate their workforce to more value-added tasks, such as customer service and business development, further enhancing their competitive position in the market.
The cost-efficiency of hybrid printing equipment extends beyond immediate production expenses. By enabling print service providers to take on a wider range of jobs and offer quicker turnaround times, these systems can help businesses increase their overall revenue and profitability.
Automation features simplify hybrid press operation
The sophistication of hybrid printing equipment is matched by the advanced automation features that simplify their operation. These automation capabilities are crucial in maximizing the efficiency and effectiveness of hybrid presses, allowing print shops to handle complex jobs with ease and precision.
Modern hybrid systems come equipped with intelligent workflow management software that automates job setup, color management, and quality control processes. This level of automation ensures consistency across print runs and minimizes the potential for human error. Operators can manage multiple jobs simultaneously, with the system handling many of the technical adjustments automatically.
Automated plate changing and ink key settings in the offset components of hybrid presses significantly reduce setup times between jobs. Meanwhile, digital components benefit from automated calibration routines
that maintain color accuracy and print quality without manual intervention.
These automation features not only simplify press operation but also contribute to the overall flexibility and responsiveness of print production. Printers can quickly adapt to changing job requirements and maintain high levels of productivity even with a diverse mix of print orders.
The advanced automation in hybrid printing systems empowers operators to focus on higher-level tasks, driving innovation and customer satisfaction in print production.
Hybrid equipment expands print application possibilities
The versatility of hybrid printing equipment opens up a world of new possibilities for print applications. By combining different printing technologies, these systems enable print service providers to offer a broader range of products and services to their clients, often venturing into new market segments.
Unique substrates open new markets
Hybrid presses are capable of handling a wide variety of substrates, from traditional paper stocks to specialty materials like synthetic papers, plastics, and even metallic foils. This substrate flexibility allows printers to expand their product offerings into areas such as packaging, labels, and industrial printing applications.
For example, a hybrid press might use its digital component to print variable data on a plastic substrate, followed by an offset unit applying a consistent background color, and finally, a flexographic unit adding a protective coating—all in a single pass. This capability to work with diverse materials opens up new market opportunities and revenue streams for print businesses.
Value-added embellishments attract brand owners
Many hybrid printing systems incorporate inline embellishment options that add significant value to printed products. These can include:
- Spot UV varnishing for highlighting specific areas
- Foil stamping for metallic effects
- Embossing and debossing for tactile elements
- Specialty coatings for unique finishes
These value-added features are particularly attractive to brand owners looking to create premium packaging or marketing materials that stand out in a crowded marketplace. By offering these embellishments as part of an integrated printing process, print service providers can differentiate themselves and command higher margins for their products.
Security printing capabilities broaden offerings
The combination of digital and conventional printing technologies in hybrid systems makes them ideal for security printing applications. These presses can incorporate various security features into printed materials, such as:
- Microtext and fine-line patterns
- Variable data QR codes for track and trace
- Invisible UV inks for covert security elements
- Holographic effects and color-shifting inks
This capability to produce secure documents and packaging opens up opportunities in sectors such as pharmaceuticals, government, and high-value consumer goods. Print service providers equipped with hybrid presses can offer comprehensive security printing solutions that were previously only available through specialized equipment.
The expanded application possibilities of hybrid printing equipment not only diversify a printer's product portfolio but also position them as innovative solution providers in the eyes of their clients. This versatility is key to staying competitive in an evolving print market where customization and added value are increasingly important.
As the printing industry continues to evolve, hybrid equipment stands out as a forward-thinking investment. Its ability to combine the strengths of various printing technologies while offering enhanced automation and versatility makes it an attractive option for print service providers looking to future-proof their operations. By embracing hybrid printing systems, businesses can position themselves at the forefront of print innovation, ready to meet the diverse and changing needs of their clients in an increasingly dynamic market.